مشکلات و چالش های سیستم های هیدرولیک
سیستمهای هیدرولیک به عنوان یکی از اجزای حیاتی بسیاری از ماشینآلات صنعتی نقش بسزایی در عملکرد دقیق و کارآمد آنها ایفا میکنند با این حال سیستمهای هیدرولیک علیرغم مزایای فراوان با برخی مشکلات و چالشها نیز همراه هستند. درک این چالشها به مهندسان و تکنسینها کمک میکند تا سیستمهای هیدرولیک را بهتر طراحی نگهداری و عیبیابی کنند. در ادامه به برخی از مهمترین مشکلات و چالشهای سیستمهای هیدرولیک اشاره میشود:
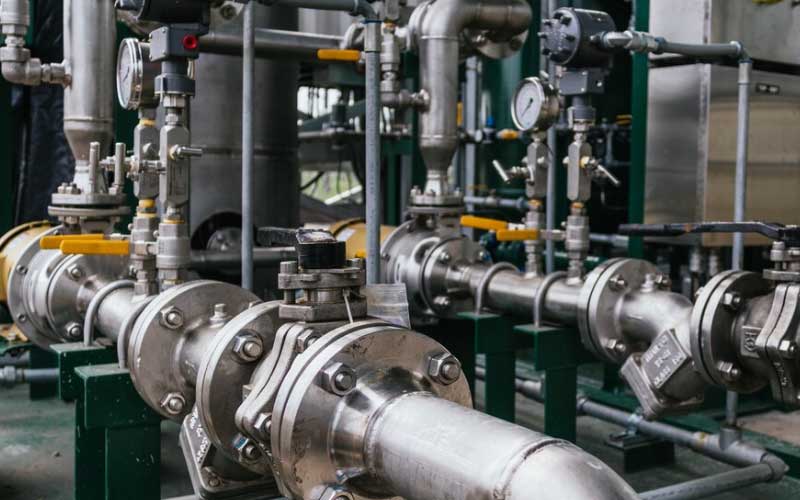
- آلودگی روغن هیدرولیک: ورود ذرات خارجی رطوبت یا مواد شیمیایی به روغن میتواند باعث سایش زودرس قطعات مسدود شدن مجاری و کاهش کارایی سیستم شود. برای جلوگیری از این مشکل استفاده از فیلترهای با کیفیت تعویض به موقع روغن و رعایت اصول بهداشتی در هنگام کار با سیستم ضروری است.
- نشت روغن: نشتی روغن از اتصالات و واشرها میتواند منجر به کاهش فشار آلودگی محیط کار و کاهش عمر مفید روغن شود. برای رفع این مشکل استفاده از واشرها و اتصالات با کیفیت بررسی منظم اتصالات و تعویض به موقع آنها توصیه میشود.
- گرم شدن بیش از حد روغن: افزایش دمای روغن میتواند باعث کاهش ویسکوزیته تشکیل رسوبات و کاهش عمر مفید روغن شود. برای جلوگیری از این مشکل استفاده از خنککنندههای روغن طراحی مناسب سیستم و رعایت ظرفیت کاری تجهیزات ضروری است.
- کویتاسیون: تشکیل حبابهای هوا در روغن میتواند باعث ایجاد صدا لرزش و آسیب به پمپ شود. برای جلوگیری از کویتاسیون طراحی مناسب سیستم استفاده از پمپهای با کیفیت و اطمینان از پر بودن مخزن روغن از اهمیت ویژهای برخوردار است.
- پیری روغن: با گذشت زمان روغن هیدرولیک خواص خود را از دست داده و باعث کاهش کارایی سیستم میشود. برای رفع این مشکل تعویض به موقع روغن با توجه به دستورالعملهای سازنده الزامی است.
بررسی عمیقتر عوامل مؤثر در بروز مشکلات در سیستمهای هیدرولیک
عوامل ذکر شده از جمله مهمترین دلایل بروز مشکلات در سیستمهای هیدرولیک هستند. اجازه دهید دیگر عوامل را به طور مفصلتر و با دید تخصصی بررسی کنیم:
عوامل مؤثر بر بروز مشکلات:
-
طراحی نامناسب سیستم:
- انتخاب نادرست اجزای سیستم: استفاده از قطعاتی که با مشخصات فنی سیستم همخوانی نداشته باشند میتواند به عملکرد نامطلوب و خرابی زودهنگام منجر شود.
- محاسبات نادرست: خطا در محاسبات پارامترهایی مانند فشار دبی و افت فشار میتواند به بروز مشکلاتی همچون کاویتاسیون و نشت روغن منجر گردد.
- طراحی نامناسب مسیر لولهها: طراحی نامناسب مسیر لولهها از نظر طول قطر و تعداد زانوها میتواند به افزایش افت فشار کاهش سرعت پاسخدهی سیستم و ایجاد نقاط تجمع هوا منجر شود.
-
انتخاب تجهیزات نامناسب:
- پمپ: انتخاب پمپ با ظرفیت نامناسب نوع روغن نامناسب یا نصب نادرست میتواند به کاهش کارایی افزایش مصرف انرژی و خرابی زودهنگام منجر شود.
- شیرها: انتخاب شیرهای نامناسب از نظر نوع اندازه و جنس میتواند به نشت روغن کاهش دقت کنترل و افزایش افت فشار منجر شود.
- سیلندرها: انتخاب سیلندر با قطر و کورس نامناسب یا استفاده از آببندهای نامناسب میتواند باعث کاهش نیروی خروجی نشت روغن و افزایش اصطکاک شود.
- فیلترها: استفاده از فیلترهای با دقت فیلتراسیون نامناسب یا نصب نادرست میتواند باعث آلودگی روغن و آسیب به سایر اجزای سیستم شود.
- شیلنگ هیدرولیک: شیلنگ هیدرولیک و اتصالات هیدرولیک اجزای حیاتی در هر سیستم هیدرولیکی هستند که نقش بسیار مهمی در انتقال سیال تحت فشار و عملکرد کلی سیستم ایفا میکنند. انتخاب و استفاده صحیح از این قطعات تأثیر مستقیمی بر کارایی ایمنی و طول عمر سیستم دارد.
-
عدم آموزش کافی پرسنل:
- نقص در نگهداری و تعمیرات: عدم آشنایی پرسنل با روشهای صحیح نگهداری و تعمیرات میتواند به بروز مشکلات مختلفی همچون آلودگی روغن نشت روغن و خرابی زودهنگام تجهیزات منجر شود.
- عیبیابی نادرست: عدم توانایی پرسنل در تشخیص و رفع مشکلات میتواند باعث توقف طولانی مدت تولید و افزایش هزینههای تعمیر شود.
- خطای انسانی: خطاهای انسانی در هنگام کار با سیستمهای هیدرولیک میتواند باعث آسیب به تجهیزات و ایجاد خطر برای پرسنل شود.
راهکارهای بهبود عملکرد سیستمهای هیدرولیک:
-
- برنامهریزی منظم برای نگهداری: اجرای بازرسیهای دورهای تعویض به موقع روغن و فیلترها و بررسی وضعیت کلی سیستم از جمله اقدامات اساسی در نگهداری پیشگیرانه محسوب میشود.
- بهینهسازی طراحی سیستم: با استفاده از نرمافزارهای شبیهسازی و محاسبات دقیق میتوان به طراحی بهینه سیستمهای هیدرولیک دست یافت و از بروز مشکلات ناشی از طراحی نامناسب جلوگیری کرد.
- انتخاب تجهیزات با کیفیت بالا: استفاده از پمپها شیرها سیلندرها و سایر تجهیزات با کیفیت و مطابق با استانداردهای صنعتی نقش مهمی در افزایش عمر مفید سیستم دارد.
- آموزش تخصصی پرسنل: برگزاری دورههای آموزشی تخصصی برای پرسنل عملیاتی و تعمیرات به منظور افزایش دانش و مهارت آنها در زمینه نگهداری و عیبیابی سیستمهای هیدرولیک ضروری است.
- کنترل کیفیت روغن: انجام آزمایشهای دورهای بر روی روغن هیدرولیک برای اطمینان از حفظ خواص فیزیکی و شیمیایی آن از اهمیت بالایی برخوردار است.
- بهبود سیستم خنککاری: طراحی مناسب سیستم خنککاری و استفاده از خنککنندههای روغن به جلوگیری از افزایش دمای روغن و کاهش ویسکوزیته آن کمک میکند.
- استفاده از فناوریهای نوین: بهرهگیری از سنسورها سیستمهای مانیتورینگ و تشخیص هوشمند عیب امکان نظارت بر وضعیت سیستم و تشخیص زودهنگام مشکلات را فراهم میآورد.
- کاهش اصطکاک: استفاده از روانکارهای با کیفیت بالا و طراحی سطوح تماس به گونهای که اصطکاک به حداقل برسد به کاهش سایش قطعات و افزایش عمر مفید آنها کمک میکند.
با اجرای دقیق این راهکارها میتوان به نتایج زیر دست یافت:
- افزایش طول عمر مفید سیستم: با کاهش سایش و خوردگی قطعات طول عمر مفید سیستمهای هیدرولیک به طور قابل توجهی افزایش مییابد.
- کاهش هزینههای تعمیرات: با تشخیص و رفع زودهنگام مشکلات از بروز خرابیهای بزرگ و هزینههای سنگین تعمیرات جلوگیری میشود.
- افزایش بهرهوری: عملکرد پایدار و قابل اطمینان سیستمهای هیدرولیک به افزایش بهرهوری و کاهش زمان توقف تولید منجر میشود.
- کاهش مصرف انرژی: با بهینهسازی عملکرد سیستم میتوان به کاهش مصرف انرژی و هزینههای عملیاتی دست یافت.
نتیجهگیری
سیستمهای هیدرولیک به عنوان یکی از اجزای حیاتی ماشینآلات صنعتی نیازمند توجه ویژه و نگهداری مناسب میباشند. با اتخاذ رویکردهای پیشگیرانه و اجرای راهکارهای فنی مناسب میتوان به عملکرد بهینه و طول عمر بالای این سیستمها دست یافت.
آیا شما به دنبال کسب اطلاعات بیشتر در مورد "مشکلات و چالش های سیستم های هیدرولیک" هستید؟ با کلیک بر روی اقتصادی, کسب و کار ایرانی، آیا به دنبال موضوعات مشابهی هستید؟ برای کشف محتواهای بیشتر، از منوی جستجو استفاده کنید. همچنین، ممکن است در این دسته بندی، سریال ها، فیلم ها، کتاب ها و مقالات مفیدی نیز برای شما قرار داشته باشند. بنابراین، همین حالا برای کشف دنیای جذاب و گسترده ی محتواهای مرتبط با "مشکلات و چالش های سیستم های هیدرولیک"، کلیک کنید.